Công nghệ sản xuất gạch bê tông khí chưng áp
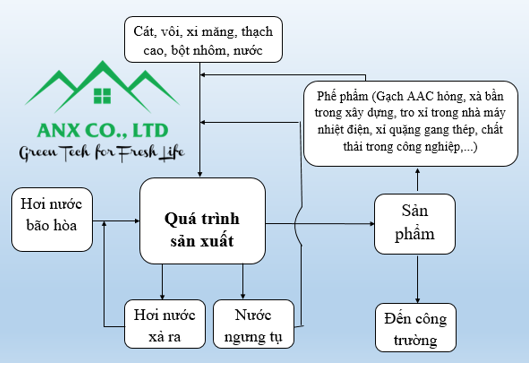
- Chuẩn bị nguyên liệu:
Các nguyên liệu chính để sản xuất gạch bê tông nhẹ gồm xi măng, vôi, tro bay, cát được đưa lên silo và bunke chứa. Cát được nghiền mịn bằng máy nghiền bi độ mịn 10 – 25%. Vôi và thạch cao được nghiền bằng máy nghiền đứng hoặc nghiền bi độ mịn 10 – 20%.
- Chế tạo huyền phù bột nhôm:
Bột nhôm, nước và phụ gia hoạt tính được định lượng và khuấy đều tạo thành lớp huyền phù bột nhôm rồi chuyển vào máy trộn. Quá trình này diễn ra song song với chuẩn bị nguyên liệu.
- Định lượng và phối trộn liệu:
Hỗn hợp nguyên liệu được đổ vào máy trộn từ 2 – 3 phút sau đó thêm huyền phù bột nhôm vào trộn thêm 1 – 2 phút. Nước được thêm vào để đạt khối lượng thể tích yêu cầu cho 1 khuôn.
- Tạo hình và dưỡng ẩm sơ bộ:
Sau khi trộn, hỗn hợp bê tông khí được đổ vào khuôn có kích thước từ 4 – 6m; rộng từ 2 – 2,5m; cao từ 0,6 – 1m. Hỗn hợp bê tông khí được đổ thấp hơn miệng khuôn từ 0,2 – 0,3m. Nếu chế tạo sản phẩm tấm panel bê tông 3D có cốt thép thì cần làm thẳng cốt thép, hàn, phủ lớp chống ăn mòn và đặt vào khuôn trước khi đổ hỗn hợp vào.
Phản ứng của bột nhôm với vôi sẽ diễn ra trong 30 phút và hết nở. Thời gian tháo khuôn phụ thuộc vào nhiệt độ môi trường và nhiệt độ hỗn hợp. Thông thường thời gian từ khi đổ khuôn đến khi tháo khuôn khoảng từ 120 – 180 phút. Trên khuôn có các gờ, móc để việc tháo lắp thuận lợi. Sau khi bê tông đạt cường độ, tiến hành tháo khuôn. Chỉ tháo 3 trong số 4 thành xung quanh.
Nghiêng khuôn và khối thành phẩm một góc 90o để thành khuôn lật xuống đáy khối bán thành phẩm. Đầu tiên, cắt bỏ phần bê tông nở quá trên miệng khuôn và đưa ngay về bể huyền phù để tái sản xuất. Máy cắt ngang và máy cắt dọc cắt khối bán thành phẩm còn lại thành từng viên theo kích thước yêu cầu.
- Chưng áp và tháo dỡ gạch:
Chưng áp là một công đoạn công nghệ quan trọng quyết định độ bền cơ học của sản phẩm. Khối bán thành phẩm được đưa lên xe goòng và đẩy vào buồng chưng áp. Đường kính của buồng chưng áp từ 2,5 – 3,5m; chiều dài từ 28 – 35m.
Sau khi xếp đầy buồng chưng áp được đậy kín, bắt đầu thời gian chưng áp. Để đạt áp suất yêu cầu từ 10 – 14atm sẽ cần khoảng 2 giờ đồng hồ. Áp suất và nhiệt độ cao được duy trì trong suốt 8 giờ. Thời gian hạ áp suất về ấp suất khí quyển là 2 giờ.
Mỗi ngày đêm một buồng chưng áp sẽ thực hiện 2 chu kỳ chưng áp. Các buồng chưng áp này hoạt động so le, buồng này tăng áp thì buồng khác sẽ hạ áp để đảm bảo công suất nồi hơi.
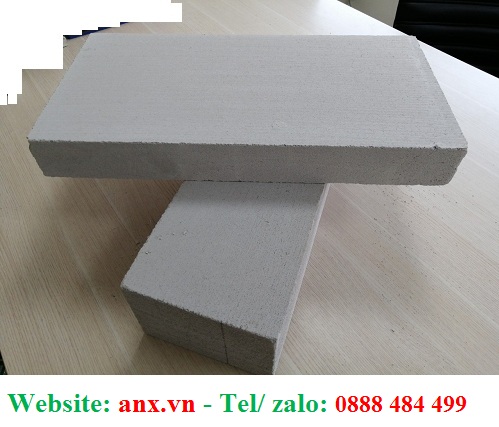
Ngoài ra, gạch không nung còn có thể sản xuất từ 1 số nguyên liệu khác như:
Sản xuất gạch không nung từ đất đá thải
Khi chọn được loại đất đá thải để sản xuất gạch người ta sẽ sấy khô còn khoảng 10 – 15% độ ẩm.
Đất sau khi sấy khô sẽ được nghiền bằng thiết bị nghiền trộn liên hợp và trộn cùng một số phụ gia khác theo chuẩn quy định, trong đó đất chiếm đến 80%.
Ủ hỗn hợp đất vừa trộn với 15 – 18% vôi, chú ý nền xưởng phải được lát bằng xi măng hoặc bê tông. Sau khi đất đã được ủ xong chúng ta sẽ tiến hành ủ cát, những chất thải xây dựng và một số loại phụ gia.
Sử dụng máy ép gạch để ép định hình viên gạch với áp lực 55 – 65MPa. Công đoạn này là quan trọng nhất trong quá trình sản xuất gạch, để đảm bảo chất lượng viên gạch cần thực hiện đúng kỹ thuật và lực ép.
Sản xuất gạch không nung từ đá mạt
Gạch không nung ngoài sử dụng đất đá thải để sản xuất người ta cũng có thể sử dụng mạt đá và xi măng để tạo thành. Việc sử dụng xi măng, mạt đá sẽ dễ thực hiện hơn loại vật liệu trên bởi có những thiết bị chuyên dụng để sản xuất.
Những nguyên liệu như mạt đá, nước, xi măng sẽ được đưa vào máy và được trộn theo thời gian đã cài đặt sẵn trên máy trộn. Tiếp đó sẽ được đưa vào hệ nạp liệu để xuống khuôn ép.
Máy ép thủy lực định hình viên gạch một cách đồng đều. Việc này sẽ giúp viên gạch có được độ ổn định cao và đạt chất lượng tốt nhất. Lực ép khoảng 18 – 20MPa.
Sau khi đã được ép chặt, gạch sẽ được chuyển ra sân phơi, trong quá trình phơi nên phun nước để dưỡng hộ nhằm giúp viên gạch cứng và chắc hơn.
Sản xuất gạch không nung tự dưỡng
Nguyên liệu chủ yếu sản xuất gạch sử dụng các phế thải công nghiệp như: Bột tro bay, xỉ lò phối trộn cùng với các loại gạch ngói phế thải cũ, bột đá, cát sông, các loại cặn quặng, … và những vật liệu phụ trợ khác như vôi, xi măng, thạch cao.
Công nghệ sản xuất gạch phế liệu tự dưỡng đơn giản, lưu trình như sau: Trộn nguyên liệu (thiết bị đưa liệu hoặc đai truyền) → Máy ép gạch → Phôi → Dưỡng hộ → Thành phẩm. Theo thông thường, nguyên vật liệu được máy trộn đều, nguyên liệu được đai truyền chuyển đến máy bánh lăn để tiến hành trộn lần 2 khoảng 3 – 4 phút, sau đó được đai truyền hoặc máy đưa liệu chuyển đến trong gầu ép gạch để tiến hành ép, đồng thời gạch được công nhân vận chuyên đến xe đẩy, chuyển vào xưởng, dưỡng hộ 15 ngày sẽ trở thành thành phẩm xuất xưởng.
Gạch sử dụng chất phế thải tự dưỡng đạt chất lượng tương đối tốt, đạt mác M100 – 200, cường độ chịu nén là 3 – 4MPa, độ hút nước là 5,2 – 6,3%.
Mọi chi tiết đặt hàng, tư vấn thiết kế, quý khách vui lòng gửi thông tiến đến chúng tôi qua:
Tel/ zalo: 0888 484 499
Email:[email protected]
Website: anx.vn
Nhân viên công ty tiếp nhận trả lời và báo giá sản phẩm liên tục trong ngày.